The Main Principles Of Turbochargers
Table of ContentsEverything about TurbochargersTurbochargers Fundamentals ExplainedSome Of Turbochargers
Forced induction device for internal combustion engines A turbocharger, colloquially called a turbo, is a turbine- driven, required induction device that increases an internal combustion engine's effectiveness and power output by requiring additional compressed air into the combustion chamber. This enhancement over a naturally aspirated engine's power output is due to the fact that the compressor can force more airand proportionately more fuelinto the combustion chamber than climatic pressure (and for that matter, ram air consumption) alone - turbochargers.Today, the term "supercharger" is usually used only to mechanically driven forced induction gadgets. The crucial difference in between a turbocharger and a traditional supercharger is that a supercharger is mechanically driven by the engine, typically through a belt connected to the crankshaft, whereas a turbocharger is powered by a turbine driven by the engine's exhaust gas.

Twincharger refers to an engine with both a supercharger and a turbocharger. Manufacturers frequently utilize turbochargers in truck, automobile, train, airplane, and construction-equipment engines. They are frequently used with Otto cycle and Diesel cycle internal combustion engines. Required induction go back to the late 19th century, when Gottlieb Daimler patented the technique of utilizing a gear-driven pump to require air into an internal combustion engine in 1885.
This patent was for a compound radial engine with an exhaust-driven axial flow turbine and compressor mounted on a typical shaft. The first prototype was finished in 1915 with the goal of getting rid of the power loss experienced by airplane engines due to the decreased density of air at high elevations.
Another early patent for turbochargers was obtained in 1916 by French steam turbine developer Auguste Rateau, for their meant usage on the Renault engines utilized by French fighter aircrafts. Separately, 1917 testing by the American National Advisory Committee for Aeronautics and Sanford Alexander Moss revealed that a turbocharger might make it possible for an engine to avoid any power loss (compared with the power produced at sea level) at an altitude of up to 4,250 m (13,944 ft) above sea level.
The very first industrial application of a turbocharger was in 1925, when Alfred Bchi successfully installed turbochargers on ten-cylinder diesel engines, increasing the power output from 1,300 to 1,860 kilowatts (1,750 to 2,500 hp). This engine was used by the German Ministry of Transportation for two big guest ships called the "Preussen" and "Hansestadt Danzig".
Turbochargers Things To Know Before You Get This
Turbochargers were used on numerous aircraft engines during World War II, beginning with the Boeing B-17 Flying Fortress in 1938, which used turbochargers produced by General Electric. Other early turbocharged airplanes included the B-24 Liberator, P-38 Lightning, P-47 Thunderbolt and the speculative Focke-Wulf Fw 190 prototypes. Car and truck producers began research study into turbocharged find here engines during the 1950s, however the issues of "turbo lag" and the bulky size of the turbocharger were unable to be solved at the time.
Following the 1973 oil crisis and the 1977 Clean Air Act modifications, turbocharging ended up being more typical in automobiles, as a method to lower fuel intake and exhaust emissions. In contrast to turbochargers, superchargers are mechanically driven by the engine. Belts, chains, shafts, and gears prevail approaches of powering a supercharger, positioning a mechanical load on the engine.

Adiabatic efficiency is a measure of a compressor's capability to compress air without including excess heat to that air. Even under ideal conditions, the compression procedure always results in elevated output temperature level; nevertheless, more efficient compressors produce less excess heat. Roots superchargers impart considerably more heat to the air than turbochargers.
In useful application the variation between the two can be significant, with turbochargers Web Site typically producing 15% to 30% more power based solely on the distinctions in adiabatic performance (however, due to heat transfer from the hot exhaust, significant heating does happen). By comparison, a turbocharger does not position a direct mechanical load on the engine, although turbochargers place exhaust back pressure on engines, increasing pumping losses.
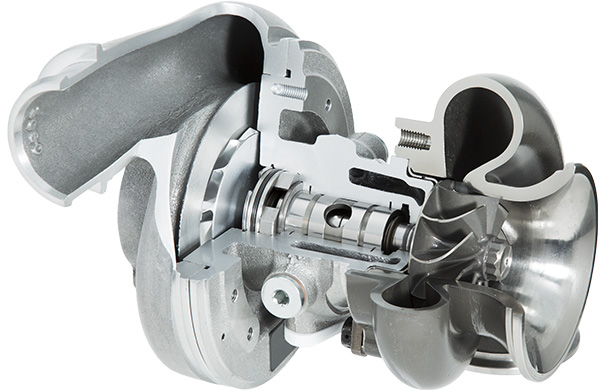
Not known Facts About Turbochargers
Only when the engine reaches adequate speed does the turbine section start to spool up, or spin quick enough to produce intake pressure above air pressure. A mix of an exhaust-driven turbocharger and an engine-driven supercharger can reduce the weaknesses of both. This method is called twincharging. In the case of Electro-Motive Diesel's two-stroke engines, the mechanically helped turbocharger is not specifically a twincharger, as the engine uses the mechanical support to charge air just at lower engine speeds and start-up.
This differs from a turbocharger that utilizes the compressor section of the turbo-compressor only during starting and, as a two-stroke engines can not naturally aspirate, and, according to SAE meanings, a two-stroke engine with a mechanically assisted compressor during idle and low throttle is considered naturally aspirated. In naturally aspirated piston engines, consumption gases are drawn or "pressed" into the engine by air pressure filling see this page the volumetric space brought on by the down stroke of the piston (which develops a low-pressure location), similar to drawing liquid using a syringe. turbochargers.
